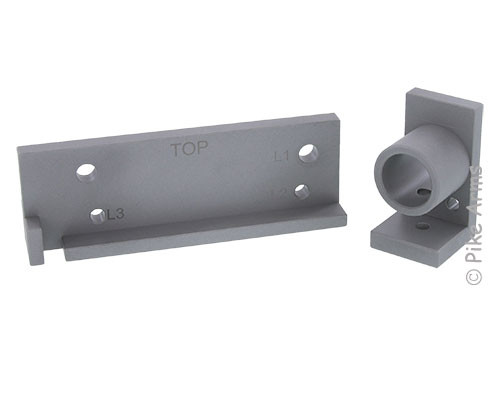
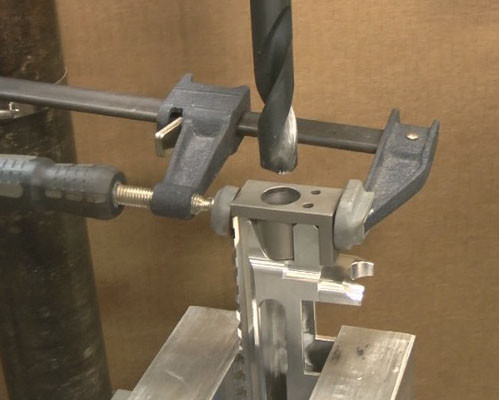
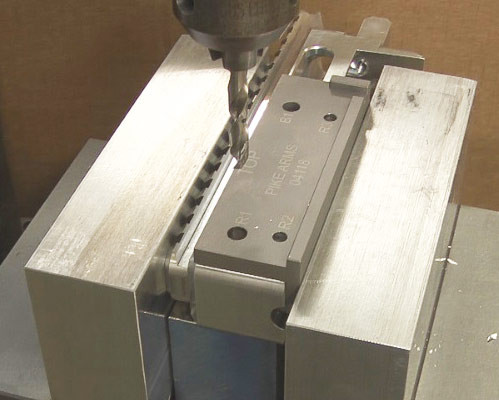
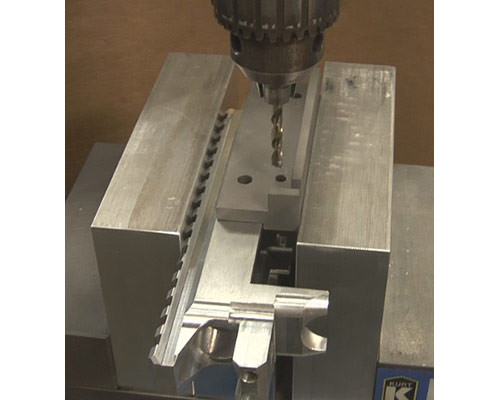
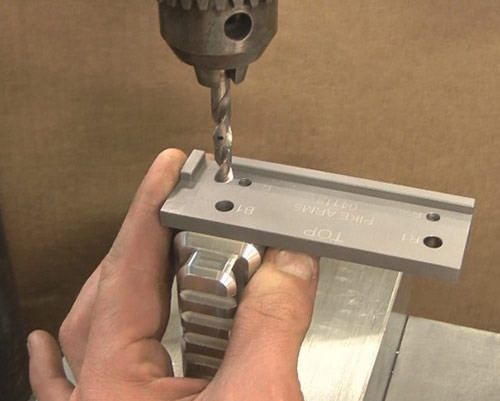
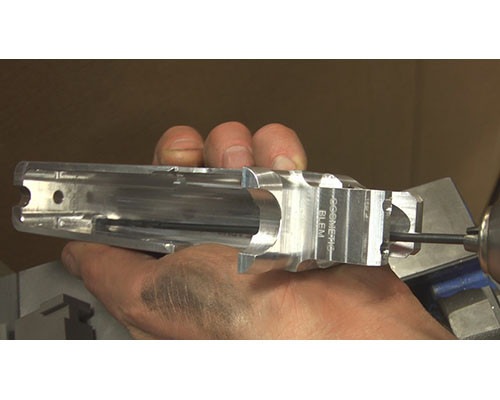
Attention
Attention
PIKE ARMS® ALUMINUM HOLE LOCATING DRILLING FIXTURE (JIG)
FOR PIKE ARMS® ELITE22TD™ TAKEDOWN "80 PERCENT" RECEIVERS
** NOT FOR ELITE22™ "80% RECEIVERS" **
For customers that only need to complete one or a couple Pike Arms®
ELITE22TD™ TAKEDOWN "80 PERCENT" Receivers, either flat top or with integral picatinny rail, this aluminum Hole Locating Drilling
Fixure will allow you to easily complete the required holes to finish your 80% receiver into a functional receiver ready for your custom build. For
customers that need to complete a quantity of receivers, we also offer
the same Hole Locating Drilling Fixture in hardened steel (part #08526).
This fixture quickly and accurately locates the following holes on a Pike Arms® ELITE22TD™ TAKEDOWN "80 Percent" Receiver:
This Aluminum Hole Locating Drilling Fixture will allow you to easily complete a Pike Arms® ELITE22TD™ Takedown receiver, in either flat top or with integral picatinny rail configuration for a custom rifle or pistol build that can then be assembled with Pike Arms® CNC precision machined parts or with Ruger® factory 10/22® parts.
NOTE 1: This fixture is made solely for use with the PIKE ARMS® 10/22® TAKEDOWN STYLE "80 PERCENT" RECEIVER BLANKS in either flat top or with integral picatinny rail configuration and will most likely not provide correct hole placement for other manufacturer's 80% receivers due to differences in the exterior dimensions.
NOTE 2: This Aluminum Hole Locating Drilling Fixture is machined from aluminum and is a wear item that is designed for one or two "drill through" uses. Repeated use will create drill guide holes that will be out of tolerance and will result in a finished receiver that is possibly not useable. For multiple drilling uses, you should instead purchase the hardened steel hole locating drilling fixture (part #08526).
NOTE 3: This fixture is ONLY for use with the Pike Arms® Elite22TD™ TAKEDOWN "80 Percent" receiver blanks and is NOT for use with the Pike Arms® ELITE22™ "80 Percent" Receiver blank (the non-takedown version). For Hole Locating Drilling Fixtures specifically for Pike Arms® ELITE22™ "80 Percent" NOT TAKEDOWN Receivers, please refer to part #08404 for aluminum or part #04118 for steel.
NOTE 4: Help Us Help You Ensure That You Have The Right Drilling Fixture:
1. This drilling fixture is ONLY for Pike Arms® TAKEDOWN 80% receivers blanks. It will work with both / either the flat top receiver or the picatinny rail receiver.
2. It will NOT work with a non-takedown Pike Arms® 80% receiver.
3. It will NOT work with other manufacturer's receivers
4. It can NOT be returned and is a final sale.
INFORMATION ON DISCONTINUED DRILLING FIXTURE COMPATIBILITY:
The discontinued takedown drilling fixture (part # 08525) will ONLY work on Pike Arms® flat top 80% receivers and should NOT be used on Pike Arms® integral picatinny rail receivers. Pike Arms 80% takedown receivers with integral picatinny rails should only be completed with this drill fixture part # 09225.
INSTRUCTIONS FOR COMPLETING THE PIKE ARMS® ELITE22TD™ "80%" RECEIVER BLANKS
In order to complete your Pike Arms® ELITE22TD™ 80% RECEIVER BLANK, you will need the following drill bits and tap:
RIGHT SIDE OF RECEIVER:
![]() ![]() |
![]() ![]() |
Place the RECEIVER JIG on the right side of the receiver with the R1, R2 etc holes visible. Ensure that the receiver jig is securely against the bottom of the receiver and also securely against the rear of the magwell. The jig should then be tightly clamped against the side of the receiver. It is preferred to use two smaller clamps that can clamp inside the receiver and then clamp the jig to the side of the receiver rather than to clamp to the other side of the receiver. USE EXTREME CAUTION if you clamp to the other side of the receiver that you do not bend or crush the receiver with the clamp. The jig should also be clamped from the bottom of the jig to the top of the receiver to ensure that it is not capable of slipping down.
NOTE when drilling holes that go though both sides of the receiver, we drill them from each side individually and not all the way through in one pass. This will help prevent misalignment.
STEP 1:
The first hole to drill is R1, which is the buffer right side hole, which is drilled with a 1/4" drill bit. Drill only through the right side of the receiver. DO NOT drill all the way though to drill the left side of the receiver.
STEP 2:
Change to a 3/16" drill bit in order to drill the trigger assembly cross pin holes, labeled on the jig as R2 and R3.
DO NOT DRILL B1 AT THIS TIME. IT IS NOT DRILLED ON THE RIGHT SIDE.
Remove the jig from the receiver. The right side of the receiver is complete.
LEFT SIDE OF RECEIVER:
![]() ![]() |
![]() ![]() |
![]() ![]() |
Now place the RECEIVER JIG on the left side of the receiver with the L1, L2 etc holes visible. Ensure that the receiver jig is securely against the bottom of the receiver and also securely against the rear of the magwell. The jig should then be tightly clamped against the side of the receiver. Clamp the jig in place identically as was done for the right side as specified above.
STEP 3:
Using the same 3/16" drill bit, drill the left side of the L2 and L3 holes for the trigger assembly cross pin holes.
STEP 4:
Change back to the 1/4" drill bit and now drill the left side of the buffer hole marked on the jig as L1.
Remove the jig from the receiver. The left side of the receiver is complete.
REAR OF RECEIVER:
The rear / back of the receiver has the ability to have a clean out hole included as an option. If you want to be able to run a rod through the receiver to push the rod out the muzzle (a preferred method) then you will have to drill the rear cleanout hole.
STEP 5:
With the rear of the receiver facing up (barrel facing the table), place the jig on the rear of the receiver with the B1 labeled hole in the center of the rear of the receiver. The jig is indexed off of the right and bottom of the receiver. Clamp the jig securely and drill a 1/4" hole.
Remove the jig. The rear of the receiver is complete.
FRONT OF RECEIVER:
![]() ![]() |
![]() ![]() |
Using the barrel portion of the jig, slide the jig into the receiver and clamp between the bottom of the jig and the top rail of the receiver.
STEP 6:
With the receiver in a vice and ensuring that it is exactly vertical and not leaning in any direction, use an 11/16" drill bit to drill the barrel hole marked F1. It is VERY important that you get this hole straight since it will determine the alignment of your barrel in the receiver. If this hole is not straight, your barrel will not ever be able to be aligned with your scope. The rear of the receiver is exactly parallel to the position that the hole needs to be drilled so you can stand the receiver on its end. Since you are going to be drilling a big hole, make sure that you have it very securely clamped in a vice before drilling the hole. This is the one step that someone with some machinist background would be very useful to have assist.
In the event you incorrectly drill the barrel hole, there is of course no way to "move" the hole or similarly "un-drill it". However, we do sell a steel bushing that can be used to save receivers that have this hole incorrectly drilled which are available in either blued finish (Part #06706) or stainless steel (Part #06707). The hole would then need to be correctly MILLED (not drilled) to the over size diameter to match the bushing and the bushing would be pressed in, resulting in a perfect barrel to receiver mating surface.
STEP 7:
With the jig in the same position, change to your #16 drill bit and drill the two cap screw holes marked F2 and F3 for the V-block cap screws. Drill these holes all the way through.
Depending on the cap screws that are used to attach the V-block as well as the length of the tap you are using, it is often requred or desired to counterbore the two threaded holes (identically to Ruger factory receivers) to allow the cap screws be screwed all the way in tightly since many do not have threads all the way to the shoulder head of the screw. If you want / need to counterborek the holes, use a 1/4" drill bit and drill into the same holes for approx .500 (half of an inch) to provide clearance for the cap screws. DO NOT over drill the holes. If you drill them too deeply to counterbore the holes you will not have enough threads left to torque the v-block cap screws and the receiver will be unusable.
STEP 8:
Using the same #16 drill bit, flip the receiver so that it is on the rail and drill the stock attaching screw hole in the bottom which is not marked on the jig.
Remove the jig. All exterior holes have been drilled and the jigs are no longer required.
STEP 9:
The last hole that needs to be drilled is the detent for the spring op rod. The spring op rod detent is a small pocket that is required in order for the op rod to stay correctly in place in the receiver when assembled.
Change your drill to the 8" long 1/8" drill bit. With the receiver standing on the rear of the receiver (same position as you used to drill the barrel hole), drill through the barrel hole all the way down to the small exposed surface and carefully spot the area for the op rod. This is a detent and not a deep hole. Do not drill this hole too deeply. You can use an op rod to "feel" if you are deep enough which is indicated by the rod securely staying in the detent and not being able to be easily pushed out of the detent.
TAP HOLES:
STEP 10:
10A. Using a 12-24 tpi tap, hand tap the two cap
screw holes for the V-block all the way through. Make sure to use oil and extreme care not to
overload the tap and snap it off in the hole (which would render the receiver
not usable). It will appear that the tap in our tooling kits is not long enough, however if you correctly conterbored the holes approximately .500 for cap screw thread clearance, then you will have more than ample tap length to thread the holes.
10B. Using the same 12-24 tap, also tap the hole for the stock attaching screw.
CLEANUP AND FINE TUNING:
1. All of the holes will be below the stock line and will not be visible when the rifle is assembled. However, if you want the drilled holes to also be black, you can use Birchwood Casey ALUMABLACK (Our Part #02210) on the holes to blacken the newly drilled holes to match a black receiver.
2. If any of the holes are too sharp, they will need to be deburred with either a larger drill bit or an exacto knife etc. All holes should be smooth at the surface.
Your receiver is now complete and may be assembled the same as any other 10/22 style receiver.
TACTICAL
INNOVATIONS’ ELITE22™
REPLACEMENT 10/22® RECEIVER
ASSEMBLY INSTRUCTIONS
Thank you for your purchase of a Tactical Innovations’ ELITE22™ receiver. The receiver is precision CNC machined from aircraft 6061 grade aluminum to provide years of reliability and pleasure. Please review these assembly instructions and tips before attempting to assemble your receiver.
The receiver can be assembled with Ruger® factory parts or a custom rifle can be assembled using our billet machined replacement parts. Parts manufactured by third party companies may also work but the use of parts from multiple different manufactures can often be problematic and require additional fitting and troubleshooting as a result of the tolerances for each part from each manufacturer.
BARREL INSTALLATION:
The barrel is installed using a V-Block and cap screws identically to the factory assembly. The shank on the barrel, regardless of the manufacturer, will be larger than the hole in the receiver and will not slip into the receiver without fitting. The receiver barrel hole is precisely machined and should not be “fitted” or modified during the assembly process; only the barrel shank should be fitted to the receiver. It is critical that the barrel shank have a light press fit into the receiver. If the barrel shank is loose in the receiver hole, then the barrel will droop when the V-block is tightened and it will be impossible to align a scope with the point of impact since the barrel will be slightly pointing down and will not be parallel with the bore.
To fit the barrel to the receiver, you will need to only remove a very small amount of material from the barrel shank (the part of the barrel that goes into the receiver hole). Do not use a dremel or similar power tool to grind on the receiver hole or the barrel shank. Use sandpaper or a flat file on the barrel shank only. One method is to roll the barrel across your lap while you use the file or sandpaper in order to ensure that you are removing the same amount of material from all sides of the barrel shank to maintain its concentricity. When fitted to the proper size, and with the barrel shank lightly oiled, you should be able to press the barrel shank into the receiver hole by hand without using a mallet or similar to hammer the barrel into the receiver. It should be tight but you should still be able remove it if necessary and be able to rotate the barrel in order to align the extractor slot with the extractor on the bolt.
With the barrel now fitted into the receiver hole, place the bolt in the receiver WITHOUT the recoil spring and with the bolt retracted for clearance, rotate the barrel so that the extractor in the bolt lines up with the extractor slot in the barrel. Use caution not to pull the extractor out of the bolt when rotating the barrel for alignment. Stand the receiver on the opposite end from the barrel and press down on the barrel into the receiver. Although a traditional V-block is often adequate, an ADJUSTABLE V-BLOCK (Part #00204) is recommended so that you can set the barrel to any angle relative to the bore. Install the V-Block and the cap screws hand tight. Torque the cap screws while pushing down on the barrel and verify that the barrel is not pulling toward the V-block as you tighten the V-Block. If the barrel is correctly fitted to the receiver hole, the barrel will not droop (ie pull toward the V-block). If it does, you will have to use an adjustable V-Block to prevent the barrel from drooping as the V-Block is tightened. Prior to the V-Block being torqued, verify that the extractor in the bolt aligns perfectly with the extractor slot in the barrel. Barrel installation is complete.
BOLT CONSIDERATIONS:
The width of the bolt is critical for safe and reliable operation. Ruger® factory bolts that have been “polished” will often then be too thin from the polishing process removing metal and a slam fire condition is possible. Do not use a Ruger® factory bolt that has been “polished” or otherwise modified in any way. When assembling your rifle, ensure that the bolt that you use is wide enough to not allow the bolt to hit the rim and fire the round if the bolt is pushed all the way to either side of the receiver. The entire rim of the round should always be in the corresponding pocket of the bolt regardless of the left or right position of the bolt in the receiver.
TROUBLE SHOOTING:
Chambering: In order for the rifle to successfully chamber the new round each time, the bolt face has to be smooth and have the correct geometry. Generally, a machined bolt will have a more uniform finish and geometry than a Ruger® factory cast bolt although cast bolts will work most of the time. The recoil spring has to have sufficient force to be able to drive the weight of the bolt forward and strip a round from the magazine. The magazine feedlips have to be designed to ensure that the feed angle will correctly present the round to the chamber. Plastic magazines often will wear out and the feed angle will change. Similarly, different brands of high capacity magazines will have different feed angle geometry resulting in one brand working well and another not working at all. In addition, the actual bullet shape of different brands of ammunition in high capacity magazines will change the feed angle relative to other brands of ammunition that have a different bullet profile. For testing, always use a Ruger® 10 round rotary magazine since the rounds are individually nested and are not stacked on top of each other.
The 10/22® rifle operates based on the blowback of the bolt by the brass when fired. In order for the rifle to function correctly, the recoil of the fired brass has to be greater than the combined resistance of (1) the weight of the bolt, (2) the force of the recoil spring (3) cocking the hammer and (4) the drag of the bolt on the receiver especially whennew, dirty or not oiled. Different brands of ammunition, especially bulk ammunition, will have lighter recoil than ammunition such as CCI® MiniMags®. Similarly, ammunition can have different blowback force from one round to the next due to powder variations in the ammunition. As a result, if the fired round does not blow the bolt all the way rearward each time, you will experience failures to feed as well as failures to eject.
Failure to Feed: When the bolt does not blow back far enough, it will not get behind the next round in the mag in order to strip and push it into the barrel. When this occurs, you will see the bolt stopped and usually dug into the lead bullet of the next round in the magazine. A similar condition, although more difficult to diagnose, occurs when the bolt does not blow back far enough each time and just barely blows back to minimally get behind the next round in the magazine, at which point you will not have the full travel and force of the bolt coming forward to strip the round out of the mag and run it into the chamber. To remedy this issue, you will have to shoot hotter ammo or reduce the countering recoil force as noted above by modifying the recoil spring.
Many third party barrel manufacturers will often use tighter chambers in an effort to increase accuracy. However, the tighter chamber (and often with no feedramp) combined with sharper edges on the chamber face, will make successfully feeding ammo from the magazine to the chamber much more difficult. To successfully feed ammunition into a tighter chamber with no feedramp and sharper edges, you may have to lightly polish the chamber end of the barrel and create a more accessible chamber for the round to be able to feed.
Stovepipe Failure: A stovepipe failure or similar with fired brass ending up jammed in the receiver is usually a function of the extractor on the bolt not pulling the fired brass out of the chamber as the bolt is recoiling to the rear of the receiver. Ideally, the brass would exit the barrel and stay on the face of the bolt without an extractor but the extractor makes sure that the brass leaves the barrel and stays on the bolt while the bolt recoils until the brass hits the ejector with enough force to be thrown out of the gun. If the extractor does not grab the brass out of the chamber or does not hold the brass on the face of the bolt, you should replace the extractor. We offer a Sharp Claw Extractor (Part # 00422 that is EDM cut and not stamped) that will cut into the brass to pull it from the receiver. Most extraction issues are due to the failure of the extractor, which is an easy and inexpensive part to replace.
A stovepipe stoppage can also occur when the bolt does not blow back far enough / hard enough for the brass to strike the ejector with enough force to kick it out of the receiver, and instead it simply falls off the bolt into the receiver. To remedy this issue, you will have to either shoot hotter ammunition or reduce the recoil resistance as noted above, with the easiest option being to clip one or two coils off the recoil spring while continuing to test after clipping each coil.
Reliable function and operation requires that all parts successfully work together as intended. Many issues can be determined and resolved by substituting known non-issue Ruger® factory parts out of the assembly one at a time until the problematic part(s) are identified. Although the majority of rifle assemblies can be completed without any issues (especially when using either all Ruger® parts or all Tactical Innovations’ parts), you should seek competent professional gunsmithing assistance should you encounter a situation that exceeds your comfort or experience level. We are happy to perform a comprehensive measurement and quality check on any of our receivers but do not offer assembly or trouble shooting gunsmithing services.